“As the COVID-19 pandemic has painfully reminded us, far too many people have been left out and left behind for far too long. . . . With this economic recovery, we have both a rare opportunity and a moral imperative to build an economy that is truly inclusive and give every person the chance to succeed. We know that when organizations are more inclusive, they are more successful. Community colleges by their very nature are inclusive and promote opportunity for all. This commitment by the Urban Manufacturing Alliance and The Century Foundation, by partnering with community colleges across the country, is helping widen the circle of opportunity and increase racial equity in the manufacturing sector.” —President Bill Clinton, founder and board chair of the Clinton Foundation
The Century Foundation (TCF) and the Urban Manufacturing Alliance (UMA) are pleased to announce the convening of the second Industry and Inclusion cohort. The second Industry and Inclusion (I&I) Cohort includes representatives from twelve community colleges who will participate in a learning community over the next two years, all focused on improving outcomes for their Black, Hispanic,1 Asian, Indigenous, women, and other underserved students and communities. As part of the cohort, these colleges, along with workforce, industry, and community partners, will collaborate to deepen the impact of their manufacturing credentialing programs and increase equity and inclusion in their local manufacturing workforce.
Over the next eighteen months, the Industry and Inclusion Cohort will work to build manufacturing ecosystems through collaborations with community leaders, workforce development organizations, K–12 educational partners, and local employers. These partnerships will support more impactful credentialing programs that not only provide skills and competencies needed for employment, but also prepare the workforce for career mobility and positive employment outcomes. The impactful credentialing model pursues relationship-building as a key strategy and centers approaches that foster belongingness and equity for workers and communities, such as trauma-informed care, cultural competency, and racially-conscious industry partnerships. The colleges participating in the cohort are poised to deliver 2,000 manufacturing credentials using the impactful credentialing approaches developed by the cohort.
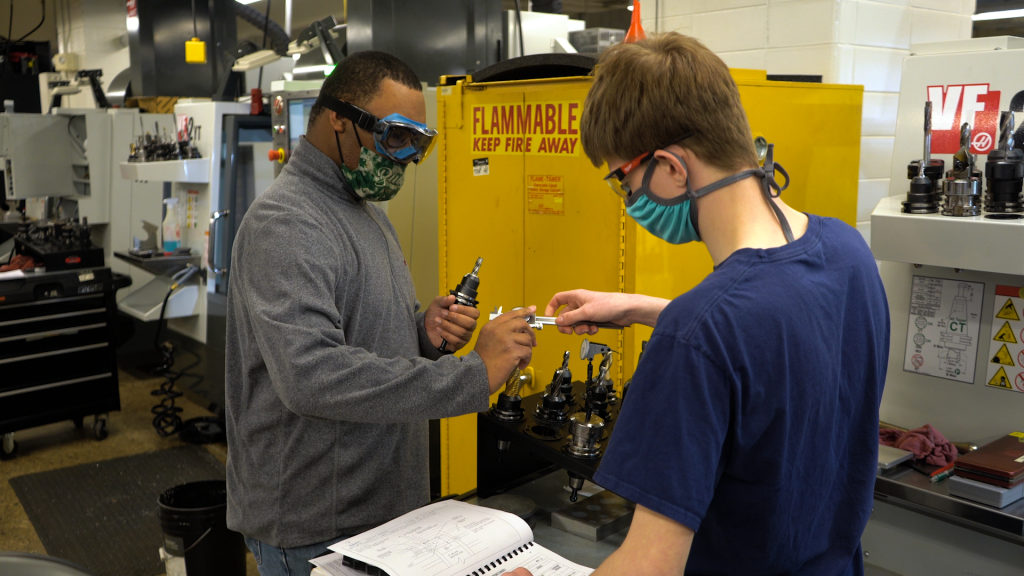
The use of impactful credentialing programs at community colleges is a critical step toward a more inclusive future for manufacturing, as community colleges are well-poised to engage and support Black, Indigenous, people of color (BIPOC), and women students in manufacturing careers. The members of this cohort will benefit from peer support and technical assistance—resources that are especially needed as they face unprecedented setbacks due to the COVID-19 pandemic and shifting employment landscape. This learning community will leverage expertise from a diverse advisory board, findings from the first Industry and Inclusion Cohort, and local partnerships to develop a set of best practices for increasing the number of students from underserved communities that successfully complete manufacturing credential programs and enter the local workforce. The Century Foundation and the Urban Manufacturing Alliance will document these best practices and identify opportunities for policymakers to support impactful credentialing in a series of publications developed out of the collaborative. Through support of the institutions in the cohort, and broader coalition-building activities in the field, the Industry and Inclusion cohort seeks to transform the industrial education paradigm across the nation.
Driving Inclusive Hiring for the Manufacturing Workforce
The manufacturing sector has rebounded rapidly from the COVID-19 pandemic, recovering all but 226,000 of 1.36 million jobs lost in Spring 2020, with the sector still, as of January 2022, adding jobs at the fastest annual pace in nearly forty years.2 Yet, the full potential of the manufacturing sector won’t be reached if it is unable to recruit the next generation of workers. Deloitte3 estimates that the sector needs to recruit 2.1 million new workers (16 percent of the current workforce) to account for job growth and retirements. Nearly every in-depth review of the nation’s industrial base4 has concluded that the shortage of skilled workers, from engineers to machinists, is a fundamental economic threat to the nation. This shortage in skilled labor comes at a time when the nation’s factories are having a harder time hiring than ever before. As Figure 1 shows, there were 9.8 million job openings over the past year, but only 5.3 million workers hired into the sector, and factories have been struggling to fill jobs in recent years even before the unique pressures of the pandemic. This inability to hire enough workers is a reversal from earlier periods, when manufacturers had more demand for jobs than they had positions to fill.
FIGURE 1
In this environment, old recruitment methods won’t suffice. On their own, individual companies are unlikely to expand the pool of talent, and instead rely mostly on poaching skilled workers from other companies. In large part, manufacturing is a specialized sector, with clusters of similar manufacturing subsectors operating in different geographies—such as automobiles in Detroit, aerospace manufacturing in Washington State, rubber in Akron, Ohio and heavy equipment in Peoria, Illinois. Thus, the best strategy is for companies to come together and identify and tackle common workforce pipeline needs through sectoral employment programs.5
Credential attainment can play a key role in these successes. A pilot program by the National Association of Manufacturers6 studying the impact of industry-recognized credentials from the National Institute of Metalworking Skills (NIMS) and the Manufacturing Skills Standards Council (MSSC) found that young adults and mid-career workers both experienced rising wages in the five years after earning a credential.
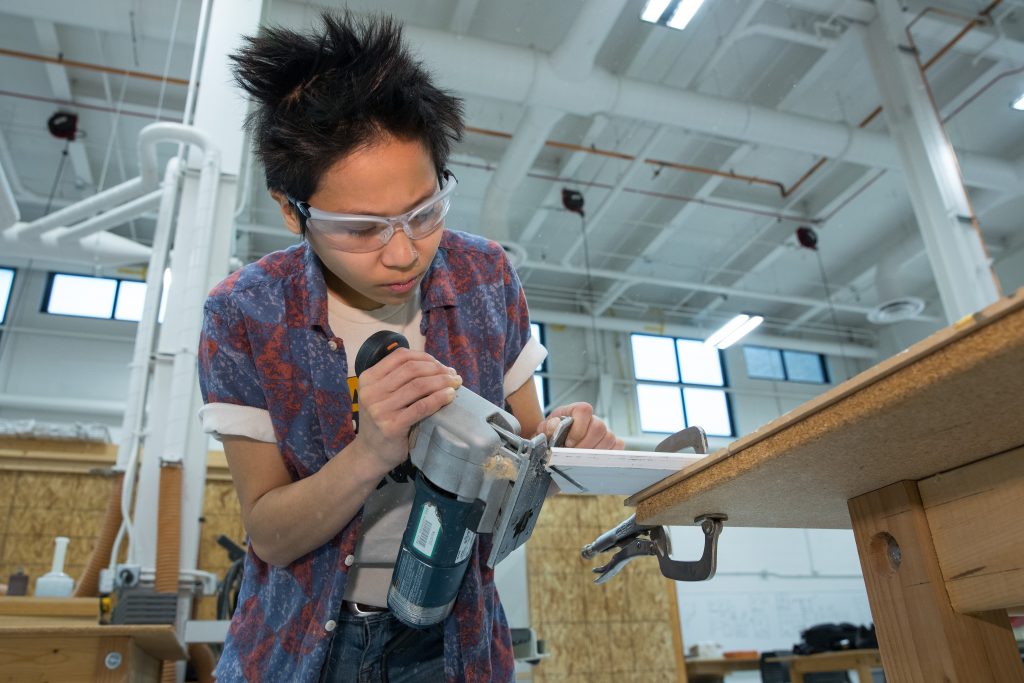
Meeting manufacturing’s workforce challenge also requires intentional approaches to diversifying the sector (see Figures 2 and 3). Unfortunately, manufacturing faces stubborn issues of gender equity and accessibility, especially for women of color, with women only making up 30 percent of the manufacturing workforce. Furthermore, nearly two-thirds of manufacturing workers are white and non-Hispanic, with smaller shares of Hispanic, Asian, and Black workers than should be achieved in 2022. For example, Black workers represent 11.9 percent of the entire workforce, but less than 10 percent of manufacturing workers—closing this gap alone would create another 300,000 jobs for Black workers.7 The Economic Policy Institute8 found that the share of Black workers in manufacturing dropped by 30 percent in the years from 1998 to 2020, a period during which Black workers lost 640,500 well-paying manufacturing jobs. And while Hispanic and Asian representation in manufacturing is on par with these population’s overall share of the workforce, that does not mean access to all jobs within the manufacturing sector is equal.
FIGURE 2
FIGURE 3
As detailed in table 1, Black and Hispanic workers employed in the manufacturing sector are far less likely to be in management or sales than white workers, and also are under-represented in installation and repair jobs, which are frequently the next step up from production jobs. These racial patterns of occupational segregation leave Black and Hispanic workers concentrated at the bottom of the manufacturing pay scale. Nearly one in four Black workers in manufacturing earns less than $30,000 per year, compared to only 15 percent of white workers in manufacturing.9
There is significant occupational segregation in manufacturing by gender as well. Women are three times more likely than men to work in administrative support positions in manufacturing, and are more concentrated in sales jobs than men. One focus group participant in the study of our first cohort—a Black woman who was a mechanic—said she “didn’t know any other Black woman who was a mechanic” working in manufacturing10; nationally, (as displayed in Table 1) less than 1 percent of women working in manufacturing work in such occupations. Meanwhile, the Institute for Women’s Policy Research found that women occupy only 7 percent of well-paid, middle-skills jobs in manufacturing,11 a worse rate than for any sector analyzed except for construction.
Table 1
Racial and Gender Representation of Workers in Occupations within the Manufacturing Sector, By Percentage of Total | |||||||
Occupation | White Non-Hispanic | Black Non-Hispanic | Hispanic | Asian | American Indian | Men | Women |
Management | 15.9 | 5.2 | 5.9 | 12.1 | 3.1 | 12.3 | 11.9 |
Business and financial | 4.3 | 2.8 | 2.0 | 4.5 | 1.6 | 2.5 | 6.8 |
Computer, engineering, and science | 12.1 | 6.9 | 5.5 | 28.5 | 9.9 | 14.2 | 8.0 |
Sales | 4.8 | 1.5 | 2.1 | 2.9 | 2.0 | 3.4 | 5.2 |
Administrative support | 9.0 | 8.1 | 7.2 | 5.9 | 9.6 | 4.6 | 17.4 |
Mechanics, installers, and repairers | 5.0 | 3.2 | 3.2 | 1.7 | 3.5 | 5.7 | 0.7 |
Production and operations | 34.5 | 52.2 | 55.7 | 37.3 | 53.3 | 40.6 | 38.7 |
Transportation and material moving | 7.2 | 12.8 | 11.4 | 3.3 | 11.1 | 9.5 | 5.4 |
Other | 6.2 | 6.3 | 7.0 | 3.8 | 5.9 | 6.2 | 5.9 |
Source: Authors’ analysis of IPUMS Current Population Survey data.
Note: Color gradient seen in PDF is based on average percentages, excluding production and operations data. Columns add up to 100 percent. |
Manufacturing still stands out in the U.S. economy as a meaningful provider of middle-class jobs. Figure 4 shows the average annual earnings of the five largest private sector industries in the economy in 2020. Manufacturing pays significantly higher than the three largest of those sectors—retail trade, education, and health services, and leisure and hospitality. Furthermore, the median earnings for workers without a four year degree in manufacturing12 is higher for Black workers ($5,000 more per year), Hispanic workers ($4,800 more per year), and white workers ($10,100 more per year) than in non-manufacturing sectors.
Figure 4
The wage advantage of manufacturing jobs is not as consistent as it once was. Economist Larry Mishel found that “the wage advantage of workers employed in manufacturing fell from 14.7 percent to 10.4 percent in the 2010s.”13 Credentialing programs can’t count on all manufacturing jobs having a pay advantage over similar jobs, and must pick their employer partners thoughtfully. A large part of the decline in manufacturing’s relative wage advantage has been the declining rate of unionization in the sector, which is down from 15.5 percent in 2001 to 8.5 percent in 2021.14 Choosing a unionized partner remains one of best ways for workforce partners to create pathways to good jobs, including but not limited to registered apprenticeships.
Finding the Way to Solve Manufacturing’s Inclusive Hiring Challenges
As outlined above, there are tremendous opportunities to drive diverse hiring to fill the workforce needs of the manufacturing sector now and into the next decade. There are also significant challenges to attracting communities that are currently underrepresented in the sector, and to tackling significant occupational segregation that exists within manufacturing. With these opportunities and challenges in mind, The Century Foundation and the Urban Manufacturing Alliance have sought to develop a replicable model of impactful credentialing. Credentialing provides a pedagogical method to impart the skills and competencies that today’s manufacturers are looking for. Impactful credentialing ensures that the credentialing process leads to positive employment outcomes and upward mobility for diverse populations.
Credentialing provides a pedagogical method to impart the skills and competencies that today’s manufacturers are looking for. Impactful credentialing ensures that the credentialing process leads to positive employment outcomes and upward mobility for diverse populations.
Industry-recognized credentialing programs have gained credibility as an important tool for more effectively aligning and filling the need for skilled workers in manufacturing. These industry-recognized credentials include credentials that new job seekers can complete in matters of months, such as NIMS level one15 and MSSC certified production technician course,16 as well as longer-term approaches, such as the Industrial Maintenance Technician apprenticeship and up-skilling opportunities for incumbent workers. However, there is much work to be done to maximize the potential of industry credentials, particularly to bridge gaps and connect more students of color and women to sustainable career opportunities.
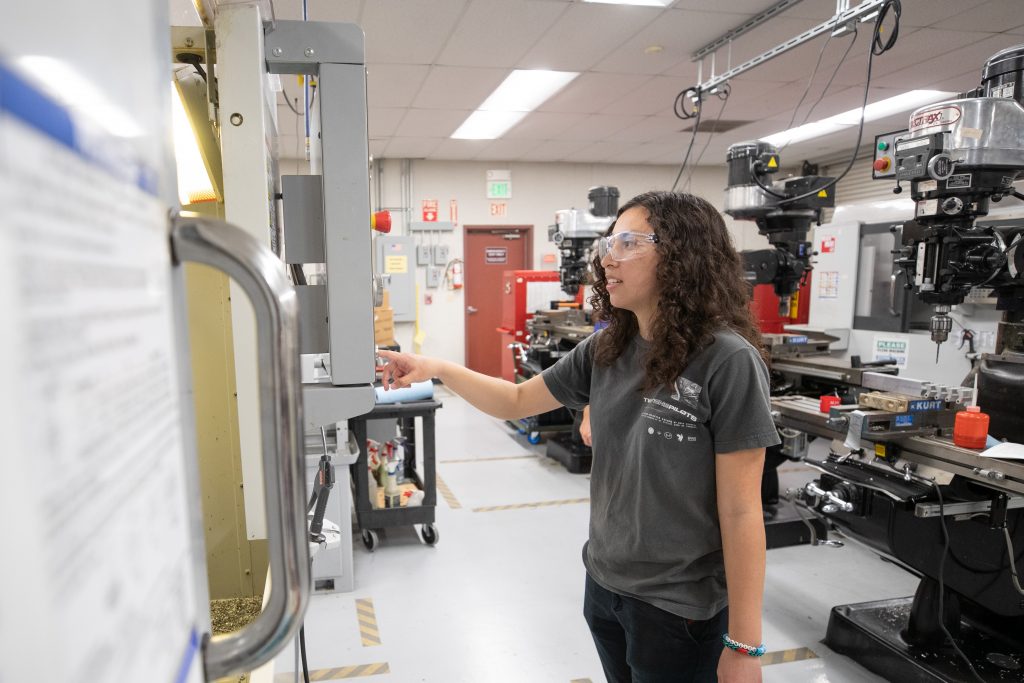
The Industry and Inclusion cohort’s work on impactful credentialing is informed by research on successful sectoral employment training programs, but leans further into diversity, equity, and inclusion and a drive to go beyond the skills gap17 into workforce and workplace change. As part of the project’s initial stage, TCF and UMA studied eight leading community-embedded workforce development practitioner organizations—all focused on connecting urban communities of color into manufacturing careers—to glean a model of impactful credentialing (see Figure 5). The findings from a year-long inquiry into these organizations (which included structured interviews between providers, and in-depth focus groups with corporate partners, students, and educators in each city) are detailed in the project’s report, “Industry and Inclusion: A Blueprint for Action.”18
FIGURE 5
Impactful credentialing programs are well-aligned and developed in collaboration with manufacturers, and situated within a broader ecosystem of support partners. These support partners include trauma-informed service providers, companies that are actively engaged in fostering racial trust and belongingness, and educators working to ensure that diverse learners are prepared for successful careers in manufacturing. Achieving more impactful credentialing will require deeper partnerships between community colleges, manufacturers, unions, and community partners—an undertaking that will demand space, external assistance, and time.
Turning to Community Colleges
Community colleges are uniquely positioned to connect more students, particularly people of color and women, to opportunities in manufacturing. Community colleges are generally the institutions with the most extensive training capacity for technical skills, in terms of both credentials produced and geographical reach. Community colleges are especially important for reaching talented Black and Hispanic students, where nearly 30 percent of those who are high achieving are students.19 Moreover, the Biden administration and Congress have proposed significant additional investments in workforce training, including a reprise of community college training partnership grants.20
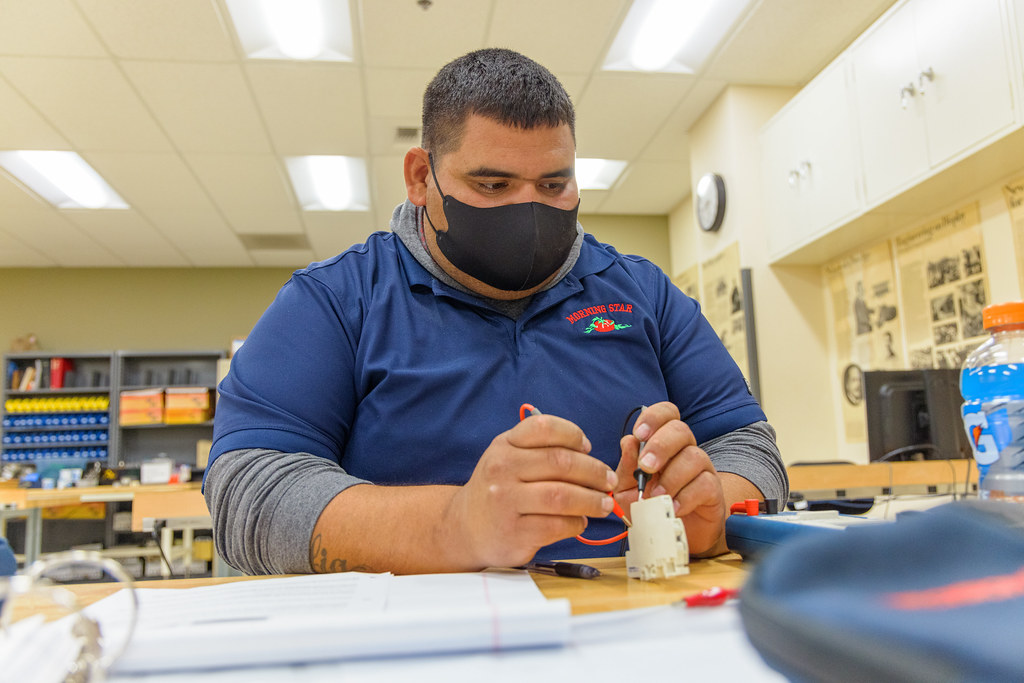
With an eye toward harnessing the capacity of community colleges, The Century Foundation and the Urban Manufacturing Alliance have expanded their Industry and Inclusion cohort to include a diverse array of community colleges. The process began with a national scan of community colleges that offered manufacturing credentialed programs. Over eighty-five community college leaders—including deans of workforce and directors of diversity, equity, and inclusion—were interviewed by the Industry and Inclusion team. In addition to identifying potential participants, the interviews established a baseline on the state of community/industry partnerships, the experiences of Black and Hispanic students, and the challenges institutions are facing. The interviews surfaced four major themes:
- Community colleges are seizing the moment on diversity, equity, and inclusion. While the vast majority of community colleges had existing commitments to advancing racial equity, the summer of 2020—which featured nationwide protests in response to the murders of George Floyd, Ahmaud Arbery, and Breonna Taylor, in particular—was a catalyst for its importance. After the protests for racial justice, community colleges explicitly published institutional commitments to further racial equity,21 which included strategies such as data-driven plans for increasing the completion rate of Black students in manufacturing programs from 50 percent to 100 percent. The challenge for the manufacturing community is to sustain the response to the racial justice awakening in 2020 into longstanding efforts to racial justice through employing cultural competence, technical assistance, and trauma-informed approaches. In particular, the colleges in the Industry and Inclusion Cohort will focus on higher enrollment and completion rates among adult learners of color.
- There is a greater understanding of why racial representation matters (among educators and industry managers) for attracting communities of color and women to manufacturing. In the words of community college interviewees for this cohort, “the students cannot be what they do not see,” and “our industry partnerships are only as good as our pipeline.”22 Having faculty and employers of color is imperative for diversifying the manufacturing pipeline, particularly women of color plant owners. We found several innovative efforts among the interviewed community colleges, such as Bishop State Community College, a Historically Black College based in Mobile, Alabama with a strong focus on representation. The college recently launched its inaugural Girls Learning About Manufacturing (GLAM) mentorship program to generate interest for women in the workforce, particularly women of color.23 Students in the program receive a mentor in supply chain management and welding technology to help them identify career opportunities in the industry.
- Manufacturing provides career mobility and can present the opportunity for previously excluded Black Americans, particularly those without a traditional four-year degree, to enter the middle class. From the enslavement of African people and their descendants, to the emergence of the Industrial Revolution, the manufacturing industry was built by the labor24 of working-class Black and white Americans, with Black Americans historically being forced to work for the lowest to no wages. Black Americans endured racism and the most dangerous jobs in manufacturing. Despite employment barriers and occupational segregation by race, manufacturing was still historically a critical entry into the twentieth-century middle class25 for the Black community. Proactive interventions can make sure that the twenty-first century revitalization of manufacturing can reestablish that path toward living-wage jobs for Black workers while charting a new course for advancement opportunities.
- Manufacturing credential programs must be responsive to the unique and holistic needs of Black and Hispanic students. Community colleges understand that without the proper holistic and wraparound supports, tangible barriers persist that prevent students from completing manufacturing programs, primarily child care and transportation needs. These barriers were only exacerbated by the pandemic, during which food and housing security, Internet access, and mental health services were also in significant demand.Manufacturing jobs present unique challenges, as students may be required to be at a manufacturing plant as early as 4:30 in the morning—arrival times that do not align with the opening of child care centers. An interviewee in St. Louis26 also informed the cohort leaders that racial and housing segregation of the city means “manufacturing is not on Black students’ radar,” and leads to transportation barriers such as commuting to a plant on another side of the city. The cohort intends to learn from programs employing holistic supports such as the Forsyth Cares program, created by cohort member Forsyth Technical Community College during the pandemic to remove nonacademic barriers in order to amplify student success.27 Forsyth Cares includes the Production Technician Program, which distributed loaner laptops, created Wi-Fi hotspots, and provided child care and rental assistance in order to support its students.
Cohort members also acknowledge that because of campus rules and practices, certain support services may be inaccessible to students who are in non-degree programs, and that is a disparity that colleges are seeking to change.
The 2022–2023 Industry and Inclusion Cohort
Community college programs are yearning to develop a true model of impactful credentialing. After the completion of the national scan, TCF and UMA selected a diverse group of twelve community colleges to join the Industry and Inclusion cohort from a competitive application process. The colleges were selected with an eye toward geographic diversity and diversity in size and approach, enabling us to glean lessons that are widely applicable (see Figure 6).
figure 6
This cohort includes one Historically Black Community College and six Hispanic Serving Institutions. Collectively the cohort is poised to deliver 2,000 manufacturing credentials by September 2023, and substantially increase the number of students of color earning these credentials.
These colleges will be brought together in an active learning community, focusing on delivering credentials valued by manufacturing employers and successfully helping new workers overcome obstacles as they approach and ascend the career ladder. The learning community will tackle issues thematically: aligning educational and employer needs around industry recognized credentials, building an equity- focused manufacturing ecosystem, cultivating inclusive classrooms and workplaces, and employing trauma-informed approaches. Members of the cohort will receive tailored technical assistance on moving toward impactful credentialing, engage with a national advisory board who are experts on manufacturing and racial equity, and connect with Manufacturing Extension Partnerships (MEPs) and Manufacturing USA institutes to elevate their programs.
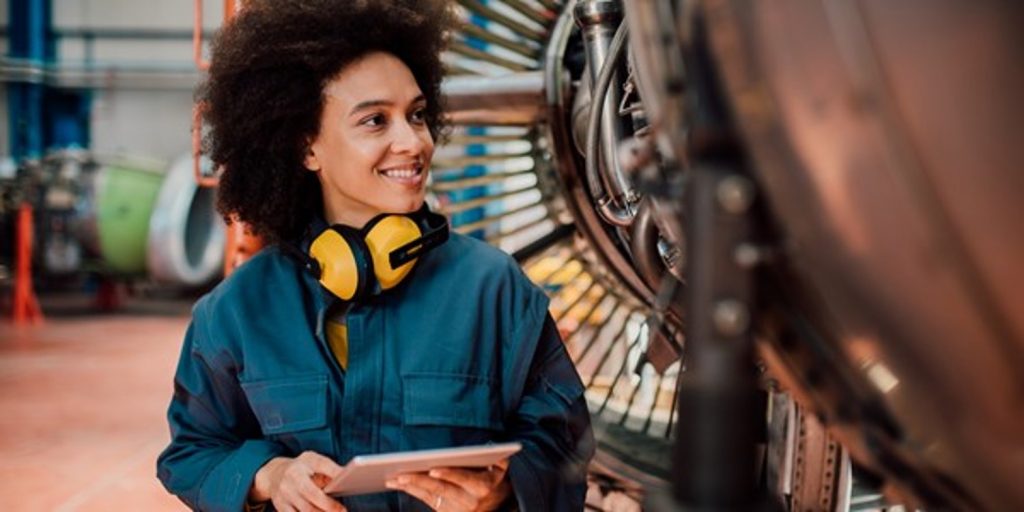
By participating in the cohort, the community colleges will strengthen equity- focused practices needed to bolster and transform their local manufacturing workforce. Our goal is for these leading institutions to incorporate these practices into their ongoing programs, supported by new federal funding streams focused on industry partnerships and the national priority of rebuilding manufacturing.
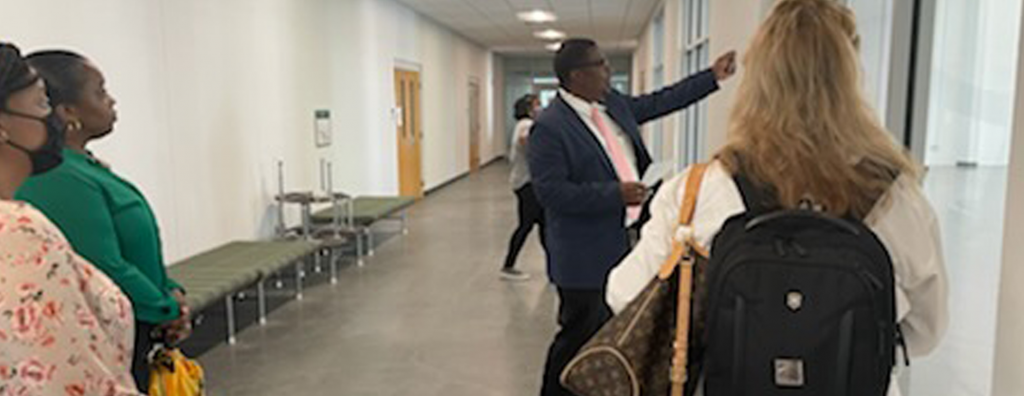
To reverberate the lessons from the cohort, TCF and UMA will publish three thematic profiles highlighting strategies and lessons deployed by the colleges in the cohort. Results from these profiles will be presented at educational conferences throughout the country over the next two years, with the aim of replicating best practices in the sector.
The Road Ahead
While the initial scan of community colleges evinced exciting practices, TCF and UMA have only scratched the surface in the investigation of college programs. While there is much to learn, it is certain that community colleges can play a transformative role in the manufacturing sector specifically and for inclusive economic growth broadly. The cohort will be another step in that direction.
About the Clinton Global Initiative
This new partnership was announced as a commitment to action through the Clinton Global Initiative’s Action Network on Inclusive Economic Recovery and Growth. The Clinton Global Initiative (CGI)28 convenes global and emerging leaders to create and implement solutions to the world’s most pressing challenges. CGI works with partners to drive action through its unique model. Rather than directly implementing projects, CGI facilitates action by helping members connect, collaborate, and develop Commitments to Action.
A Commitment to Action is a project developed and executed by an organization that addresses a pressing global issue. A commitment is a detailed project plan that includes clear and measurable objectives, a timeline and budget, and outlines the key steps required to achieve success. CGI provides a platform to collaborate and discuss these issues. This model has a proven record of success and impact—through CGI, more than 3,700 Commitments to Action have been launched, making a difference in the lives of more than 435 million people in over 180 countries.
Notes
- Throughout this report, The Century Foundation and Urban Manufacturing Alliance use Hispanic rather than Latino or Latinx. While the authors tend to prefer using Latino or Latinx when discussing ethnicity, this report uses terms that are consistent with the U.S. Census Bureau’s terms for data collection. See Mark Hugo Lopez, Jens Manuel Krogstad, and Jeffrey Passel, “Who Iis Hispanic?,”, Pew Research Center, September 21, 2021, https://www.pewresearch.org/fact-tank/2021/09/23/who-is-hispanic/.
- “All Employees, Manufacturing (MANEMP),” U.S. Bureau of Labor Statistics, retrieved from FRED, Federal Reserve Bank of St. Louis, Updated: April 1, 2022, https://fred.stlouisfed.org/series/MANEMP.
- Paul Wellener, “Deloitte and The Manufacturing Institute: Big Gains in Perceptions of US Manufacturing as Innovative, Critical and High Tech,” Deloitte, March 30, 2022, https://www2.deloitte.com/us/en/pages/about-deloitte/articles/press-releases/deloitte-and-the-manufacturing-institute-big-gains-in-perceptions-of-us-manufacturing-as-innovative-critical-high-tech.html.
- “Assessing and Strengthening the Manufacturing and Defense Industrial Base and Supply Chain Resiliency of the United States,” U.S. Department of Defense, September 2018, https://media.defense.gov/2018/oct/05/2002048904/-1/-1/1/assessing-and-strengthening-the-manufacturing-and%20defense-industrial-base-and-supply-chain-resiliency.pdf.
- Lawrence F. Katz, Jonathan Roth, Richard Hendra, and Kelsey Schaberg, “Why Do Sectoral Employment Programs Work? Lessons from WorkAdvance,” National Bureau of Economic Research, December 2020, https://www.nber.org/papers/w28248.
- “Industry Credentials’ Effect on Earning Potential: A Study of Manufacturing Data,” National Student Clearinghouse, November 4, 2020, https://www.studentclearinghouse.org/nscblog/industry-credentials-effect-on-earning-potential-a-study-of-manufacturing-data/.
- “Race in the Workplace: The Black experience in the US private sector,” McKinsey & Company, February 2021, https://www.mckinsey.com/featured-insights/diversity-and-inclusion/race-in-the-workplace-the-black-experience-in-the-us-private-sector.
- Robert E. Scott, Valerie Wilson, Jori Kandra, and Daniel Perez, “Botched policy responses to globalization have decimated manufacturing employment with often overlooked costs for Black, Brown, and other workers of color,” Economic Policy Institute, January 31, 2022, https://www.epi.org/publication/botched-policy-responses-to-globalization/.
- “Race in the Workplace: The Black experience in the US private sector,” McKinsey & Company, February 2021, https://www.mckinsey.com/featured-insights/diversity-and-inclusion/race-in-the-workplace-the-black-experience-in-the-us-private-sector.
- Andrew Stettner and Dr. Ronald C. Williams, “Industry and Inclusion: A Blueprint for Action,” The Century Foundation, June 22, 2021, https://tcf.org/content/report/industry-inclusion-blueprint-action/.
- Ariane Hegewisch, Marc Bendick Jr., Barbara Gault, and Heidi Hartmann,“Pathways to Equity: Narrowing the Wage Gap by Improving Women’s Access to Good Middle-Skill Jobs,” Institute for Women’s Policy Research, March 24, 2016, https://iwpr.org/wp-content/uploads/2020/12/Middle-skills_layout-FINAL.pdf.
- Robert E. Scott, Valerie Wilson, Jori Kandra, and Daniel Perez, “Botched policy responses to globalization have decimated manufacturing employment with often overlooked costs for Black, Brown, and other workers of color,” Economic Policy Institute, January 31, 2022, https://www.epi.org/publication/botched-policy-responses-to-globalization/.
- Lawrence Mishel, “Yes, manufacturing still provides a pay advantage, but staffing firm outsourcing is eroding it,” Economic Policy Institute, March 12, 2018, https://www.epi.org/publication/manufacturing-still-provides-a-pay-advantage-but-outsourcing-is-eroding-it/.
- Barry T. Hirsch and David A. Macpherson, “Union Membership and Coverage Database from the Current Population Survey: Note,” Industrial and Labor Relations Review 56, no. 2, (January 2003):349-54 (updated annually at unionstats.com).
- “Credentials,” NIMS, https://www.nims-skills.org/credentials.
- “Certified Production Technician,” MSSC, https://www.msscusa.org/certification/production-certification-cpt/.
- “Beyond Training and the ‘Skills Gap’ Research and Recommendations for Racially Equitable Communications in Workforce Development,” Race Forward, 2019, RaceForward_WorkforceDevelopment_BeyondTrainingAndTheSkillsGap_FullReport_2019.pdf.
- Andrew Stettner and Ronald Williams, “Industry and Inclusion: A Blueprint for Action,” The Century Foundation, June 22, 2021, https://tcf.org/content/report/industry-inclusion-blueprint-action/.
- Anthony Carnevale and Jeff Strohl, “Separate and Unequal: How Higher Education Reinforces the Intergenerational Reproduction of White Racial Privilege,” Georgetown University Public Policy Institute, Center on Education and the Workforce, July 2013, http://cew.georgetown.edu/wp-content/uploads/SeparateUnequal.FR_.pdf.
- “US Department of Labor Announces $45M Grant Funding Availability to help Close Equity Gaps, Expand Access to Training Needed for Good Paying Jobs,” U.S. Department of Labor, March 2, 2022, https://www.dol.gov/newsroom/releases/eta/eta20220302.
- Selected Community Colleges, Interviews, Summer 2021.
- Ibid.
- “Bishop State launches Girls Learning About Manufacturing (GLAM) mentorship program,” Bishop State Community College, November 3, 2021, https://www.bishop.edu/news/bishop-state-launches-girls-learning-about-manufacturing-glam-mentorship-program.
- William P. Jones, “Building America The making of the black working class,” The Nation, October 7, 2019, https://www.thenation.com/article/archive/black-working-class-history-joe-william-trotter-book-review/.
- “Restoring the Black Middle Class: Evolution of Manufacturing Jobs Requires Shift in Skill Focus,” Chicago Urban League, March 7, 2017, https://chiul.org/2017/03/10/restoring-the-black-middle-class-evolution-of-manufacturing-jobs-requires-shift-in-skill-focus/.
- St. Louis Community College, Interview with Michelle Burris, October 14, 2021.
- “Forsyth Tech CARES,” Forsyth Technical Community College, https://www.forsythtech.edu/covid-19/forsyth-tech-cares/.
- Clinton Global Initiative, https://www.clintonfoundation.org/programs/leadership-public-service/clinton-global-initiative#about/.